I think I follow a pattern when it comes to ΠWEEKs, July’s edition is mostly for software and December’s edition is much more about hardware.
7th ΠWEEK was from 15th to 19th of December so, yep, it meant “physical stuff”. Angela and I have been attending DragonCon for 4 years in a row and we enjoy every part of it, the tens of thousands of people, the talks, the panels, the shows and the amazing costumes a lot of people bring to the Con.
TL;DR Go to the video at the bottom 🙂
For 2015 we want to get into serious Cosplay too and Angela was looking forward to building up one inspired by Commander (fem)Shepard from the acclaimed Mass Effect videogame series. So the idea for this ΠWEEK was to get into wearable electronics to build a sort of biotic arm that would reflect rather sophisticated light and sound effects built in a glove.
An example of biotic energy being displayed (not the pursued cosplay/character).
The challenge was to do everything from scratch. Never before I had been faced with textile electronics, so many leds and connections, autonomous power source and acrylic thermo-manipulation.
The components used were:
- Lilypad protosnap: great arduino board meant for e-textile with 5!! PWM pins to modulate voltage as desired 🙂 Visit product link. You can use other lilypad boards but beware, this is the only one with JST and 5 PWM pins, other have less PWM pins or you need extra hardware for the battery.
- 30 blue leds (250 mcd, so reasonably bright under strong lighting). Visit product link.
- 1 accelerometer. Visit product link.
- 1 flex sensor (it came too late and wasn’t used): Visit product link.
- 1 MP3 lilypad player: Visit product link.
- 1 Conductive Thread Bobbin: We used like 2 meters. Visit product link.
- LiPo batteries: small and large like this and this.
- Cheapest Nylon Gloves: we ended up using white ones, much better to see the conductive thread.
- Acrylic sheets: for the housing of everything and to blur the lighting effects coming from the leds inside.
- A huge clay mold by Juan de la Cruz
The process was:
- Draw the schematics of the circuit: this was easy, 6 stripes of leds in parallell (5 to PWM pins, one to digital), Z on accelerometer to pin, flex sensor to pin, mp3 player T1 pin to pin.
- Write the code to trigger up to 3 modes: cooled down mode, pulsing mode, discharge mode based on accelerometer and flex sensor readings (both lighting and sound effects). This was easy too, after all, it’s arduino’s C.
- Sew everything on a single glove: this was done by Angela, I couldn’t have done it. She has the skills and electronics knowledge to make 60+ connections not touch each other while optimizing common channels on negative (-).
- Sculpt the acrylic sheet to encase the whole system: this proved to be the most challenging and unrewarding experience by far. Juan de la Cruz, a Kaleidos’ designer actually made a clay model of an arm so we could use it is a mold. It weighted 12 kilos and had intricate patterns on it, but it was impossible to use it as a mold, the acrylic sheet, even “bendy” after heated, would not allow us to easily play with it the way we needed (multiple slopes or sharp angles). BTW, best temperature is 160 Celsius, just wait 4-5 minutes and you’re ready to go.
The result was a fully functional glove with three modes (not that different between them at plain sight for the ΠWEEK demo I must admit but that is easily fixable), sound working and accelerometer working.
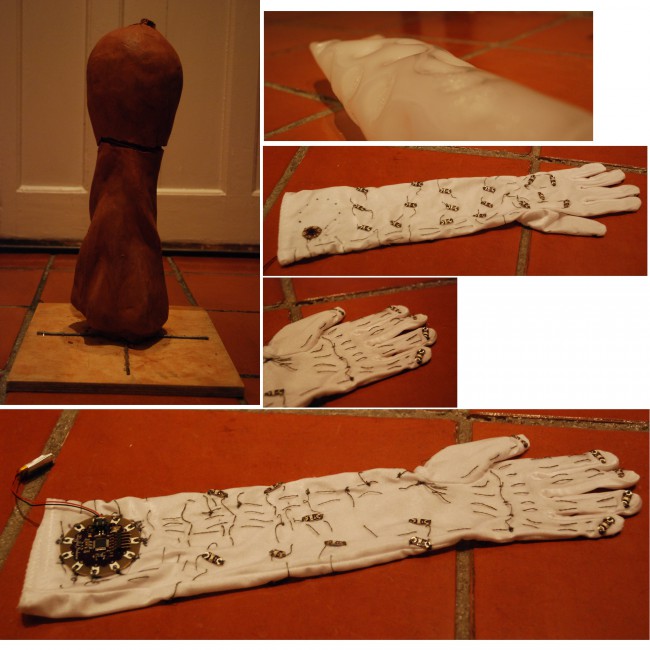
Good stuff
- Voltage drop due to the conductive thread is bearable. Leds are bright even when all 30 of them are lit up at maximum intensity.
- Accelrometer needs more callibration but Z axis works reasonably accurate for typical arm movements (up, down).
- MP3 player works great. I need to get a wearable speaker but that’s all.
- Lilypad board is capable of working great with 9 pins at minimum delays (1, 2 ms).
- The Lilypad protosnap is simply amazing, so useful for testing purposes.
Not so good stuff
- The fabric used for the gloves is crap. We need to find better fabric, more rigid while retaining elastic behavior. We will still need to use a protective glove underneath so the conductive thread does not touch the skin, when you have 1 meter of conductive thread touching your skin, those 20mA start to hurt a lot.
- Acrylic is useless here. After discarding 7 prototypes 3 and 2 mm thick and arriving to a “decent” one, it felt more like having your arm in plaster, not cool at all! We had to use a heat gun to make all the details, it was tedious and, like I said earlier, unrewarding.
Next steps
- As Juan suggested, find an alternative to the acrylic sheet. Maybe some gel or flexible translucent glove.
- Go for less wiring and maybe settle for digital versions (to control each led) of LED stips but I need to be sure it will work at 3.6V.
- Better gloves.
- Fine tuning the patterns and wearable speaker, easy.
I spent half of this ΠWEEK looking for the materials (thanks Esther for that hint on CEPLASA plastics store!), using my mother’s oven, trying to overcome the limitations of space that a glove has, etc. It was the perfect R&D into wearable electronics, now I feel confident enough to actually design the real piece of equipment for next year’s DragonCon Mass Effect cosplay for Angela 😀
You can see here the glove without and with the acrylic housing. When Angela moves her arm up and down with a gentle stroke, you can see “mode 2” in action, it is a subtle (maybe too subtle :P) wave pattern.